Colleagues:
The optikers own it. That turns out to be the answer, largely by default.
Well, servo engineering didn’t step forward. Neither did structural
engineering. Mechanical engineering and mechanical design said,
“That’s systems engineering.” The systems engineer said, “It’s
not in the requirements flow-down tree.” Program management said,
“Get me an answer!” Project engineering responded that optical
design has rules of thumb for everything, let them deal with it. And
that’s the last word I’ve heard, so far at least. So guess who’s
winning… the otpikers! It’s their industry so they take the lead, I
guess.
Now, do you remember the question? It was, “Who owns the error
budget between the gyro and the imager?” (I know, it’s been two
whole months but this is important.)
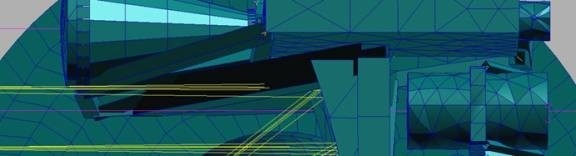
It just happens that I have what may be a
helpful (if somewhat awkward) rule of thumb for the optikers: The error
between the imager’s LOS and the gyro will be at least two or three times as
big as the error between the gyro and the resolver/encoder. This rule has
two addenda: First, improving the gyro error will not improve the LOS
error; Second, the longer you wait the harder it gets.
The AEH rule has important implications for stabilized optical instruments
(imagers, lasers, spectrometers, diffractometers, etc.): In the margin it
may be more cost effective to work to stabilize the LOS to the gyro than to
stabilize the gyro to the base (or other reference). Gasp! Take
a deep breath. You’ll be OK.
Another is that if you don’t do it early you won’t get to do it at all. Aarrrgh!
(Followed by silence.)
Just passing possibly useful insights on to my friends. AEH and AEH
Ivory are here to help.
The sunburn I picked up on Sunday was glorious (forgot my sunblock!).
Happy Summertime.
Al H.
7/12/11