The Optomechanical Constraint Equations: Theory and Applications
Author: Alson E. Hatheway
Available for purchase from SPIE Press:
http://spie.org/Publications/Book/2236945?SSO=1
PREFACE:
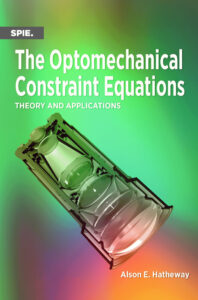
This is an engineering treatise for mechanical engineers who design and analyze optical systems. It also will be of interest to structural engineers in the optical industry and to other optics professionals. As with most engineering treatises, the book is based on both the physical science of, and the practical realities of, designing, analyzing, building, testing, and servicing real optical products.
The overwhelming majority of optical challenges that a mechanical engineer faces are associated with the position, orientation, and size of the image at the detector, the image’s first-order properties. Control of these properties throughout the mechanical design activity is essential for successful assembly and test of the first systems. If the optical elements of a system are manufactured and aligned in accordance with the dimensions in the physical optical prescription, the performance degradation due to small deviations from the prescription is dominated by misregistration of the first-order image on the detector rather than by a shift in the “balance” of the higher-order terms. The contribution of these higher-order terms (the aberrations) is usually relatively small, as shown in the following analysis of the image of a well-corrected optical system:
• It is assumed that the optical designer has given the mechanical engineer the physical optical prescription data. These data define the geometric properties of all of the optical surfaces in the system as well as the index of refraction properties for all of the materials that transmit the light. This optical prescription defines the conditions under which the optical system provides a suitable optical image, i.e., the preferred position, orientation, and size for the image, and acceptable image quality (image sharpness) over the desired field of view.
Since the optical designer’s physical optical prescription describes the conditions for the best possible optical performance, and because the mechanical engineer can neither perfectly create nor perfectly maintain those conditions in a real system, the engineer must be sensitive to the magnitude of the imaging errors being introduced by the mechanical design.
The present work deals with what are termed the first-order, or Gaussian, optical imaging effects. Gaussian imaging is specifically defined in the opening sections that discuss the nature of optical imaging and define the coordinate systems and sign conventions to be used throughout this work. These conventions are slightly different from those used by optical designers and physicists, and are based on common practice in the mechanical design arts. It is assumed that the reader has some familiarity with the physics of optical imaging from university training and perhaps some additional experience in the optical industry. The purpose of the opening sections is not so much to teach optical physics to the uninitiated but rather to adapt the optical imaging equations to the coordinate systems and sign conventions that are convenient for mechanical engineers.
What the mechanical engineer needs in order to manage the mechanical design process is the influence that each optical element has on the position, orientation, and size of the image. This treatise develops the influence functions between the positions and dimensions of all of the optical elements in an optical system and the resultant position, orientation, and size of the optical image at the detector. These functions are derived from the equations of optical imaging as adapted to the coordinate systems and sign conventions of the mechanical design.
Optical design usually begins with a defined object of interest and proceeds from there through the optical elements to the detector. The optical design assumes that the Z axis propagates with the light from the object toward the detector. Mechanical design, however, might not consider the object of the optical system at all; the object is often at infinity or some other distant location. Rather, mechanical design begins somewhere in the instrument, perhaps at the detector, and propagates outward from there, toward the incoming light. To maintain the mechanical features in a positive hemisphere, the mechanical Z axis is usually in the direction opposite that assumed in optical design, from the detector toward the system object. This work, intended for mechanical engineers, assumes sign conventions and coordinate systems convenient for mechanical design. The familiar equations of optics have been adapted to these conventions. Most of the influence functions developed here are independent of the assumed coordinate systems. Differences are noted in the text where they occur.
Some of the influence functions are linear, while others are nonlinear. The permitted deviations from the dimensions in the published physical optical prescription are usually very small. The significance of the nonlinearities diminishes quickly as the deviations (from the prescription) are reduced in size. A system is developed that segregates the linear and nonlinear components of the influence functions. This facilitates a quick solution of the linearized image motion problem but still permits the engineer to assess the magnitudes of related nonlinear effects. If they are sufficiently small, the nonlinearities might not materially reduce the margins of safety on optical performance. Otherwise, the engineer can arrange to accommodate them appropriately in the mechanical design.
The optical system’s influence functions are organized into seven equations representing the three translations, three rotations, and the change in size of the image at the detector. These equations are called the optomechanical constraint equations because they constrain the changes in the system’s image to those effects that are driven by changes in the position, orientation, and focal length of each of the optical elements. The way the equations are used is entirely up to the engineer. The influence coefficients are often used longhand or with a 10-key calculator to estimate the effects of local positioning errors during project meeting or design reviews. The optomechanical constraint equations can be developed in a computer spreadsheet program to make easy calculations for multi-element systems. Computer codes can be written that automate the preparation of the optomechanical constraint equations from the physical optical prescription data. The optomechanical constraint equations can also be imported into finite element models to evaluate the effects of elastic deflection and temperature changes in dynamic environments.
Use of the optomechanical constraint equations assumes that the Gaussian image is a reasonable proxy for the image of the system. Questions in this regard should be referred to the optical designer. The influence coefficients are presented for a number of common optical elements, and the method for convolving the individual elements into the system’s influence coefficients is shown. Finally, simple examples are provided that apply the influence coefficients to common mechanical engineering problems in optical systems.
The author hopes that the reader will find this treatise a valuable addition to the literature of optomechanics and a useful addition to the engineer’s toolbox.
Alson E. Hatheway
May 2016
REVIEWS:
This is an engineering treatise for mechanical engineers who design and analyze optical systems. It will also be of interest to other professionals working in the optics industry. The treatise is based on both the physical science and the practical realities of designing, analyzing, building, testing, and servicing real optical products.
“An important contribution to the field, this book provides engineers valuable insight into the governing parameters of optomechanical design that develop an engineer’s intuition and lead to superior design solutions.”
– Dr. Keith Doyle, MIT Lincoln Lab; Author, Integrated Optomechanical Analysis
“This book prepares the mechanical engineer to understand the importance of rigorous control of optical component location and orientation. Many figures clarify the appropriate analyses. I commend the author for his excellent presentation of the topic.”
– Paul Yoder, Author of numerous books, including Optical System Design, Field Guide to Binoculars and Scopes, Mounting Optics in Optical Instruments, Design and Mounting of Prisms and Small Mirrors in Optical Instruments, and Mounting Lenses in Optical Instruments